The Rise Of Chopper Pumps
Chopper pumps are used extensively in heavy duty solids-laden water applications including municipal waste water, industrial sewage, food processing, agricultural byproduct, and raw untreated drainage run-off from metal, paper and chemical industries. Chopper pumps increasing popularity can be attributed to the combination of increasing solids in water streams and decreasing water drain-off from residential, commercial and industrial sources. Chopper pumps solve the biggest challenge that municipalities and private waste water treatment operators face – pump clogging.
Materials Of Construction
Most chopper pumps available in the market include two sets of blades or cutters moving against one another, producing a cutting action on the solids to reduce their size. While the chopping mechanism may vary between different chopper pump manufacturers, all manufacturers recognize the need to use hard materials of construction for cutters to withstand wear and tear.
Typical cutter materials of construction include heat treated stainless steel, alloy steel and Ni-hard iron. Some shredder pumps have carbide tips on the edge of impeller vanes that have higher hardness than the base impeller material. These cutter materials supposedly have higher hardness values than most common solids found in the waste stream and are chosen to withstand reasonable levels of abrasive substances including sand, grit, mud, pebbles and small metal items.
Factors To Consider
While it is enticing to choose a cutter material with the highest hardness, it is not always the best course of action. Higher hardness is achieved by adding more Carbon to the alloy. Increasing Carbon content increases brittleness and can cause a metal component to break from an impact load. Additionally, total cost of ownership needs to be taken into consideration. What operators and engineers look for in a cutter material for a given application is its ability to last wear and tear at lowest total cost of ownership. Life expectancy of a chopper pump’s cutter is a function of cutter design, cutter material of construction, pump speed, solids loading, pump run time and service conditions. A cutter that is designed to slice solids fares better than designs that have a harsh chopping action. Cutter materials that are heat treated and have a Rockwell Hardness of at least 55 tend to wear lesser than non-hardened materials. Pumps with lower speed tend to have lower cutter wear rate than pumps with higher speed as cutting blades come in contact with solids less frequently in a lower speed pump relative to a high speed pump. The other three variables including solids loading, run time and service conditions are factors that cannot be easily controlled.
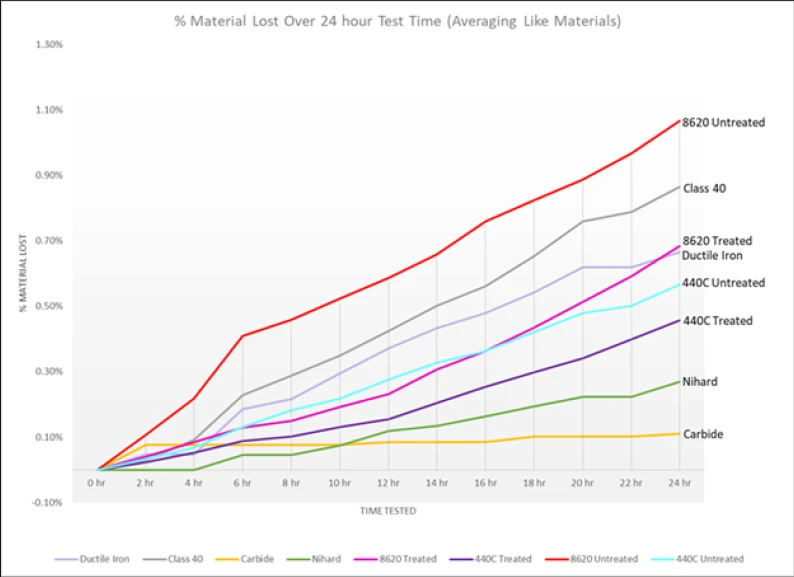
Rate Of Wear
Wear can be observed on a cutter after a few months of operation. The abrasive particles in waste water can ‘eat away’ cutter surface resulting in reduced chopping action and increased possibility of pump clogging. Rate of wear can be measured by calculating percentage of material lost over a period of time. Results from a test that analyzed rate of wear in eight different materials of construction are shown above. It confirmed that Carbide, Ni-Hard and 440C heat treated Stainless Steel are the hardest materials of construction for chopper cutters, and hence have lowest wear rates over a period of time.
Most Optimal Cutter Material
The above wear test was performed ensuring that material of construction was the only varying factor. It conclusively proved that 440C Heat Treated Stainless Steel is the most optimal material for a chopper cutter. The Heat Treated Stainless Steel has enough Carbon to have hardness of up to 60 HRC, while not being as brittle as Ni-hard or as expensive as Carbide. The 8620 treated alloy steel (also called tool steel) has a wear rate almost 40% higher than 440C Stainless Steel. As a result, cutters made from 8620 treated alloy steel last for lesser periods of time requiring more frequent and expensive cutter replacements. The advantages of 440C Heat Treated Stainless Steel over other materials of construction is evident by the use of the material in cutters in most grinder pumps in the market. There are thousands of grinder pumps with 440C stainless steel cutters that have been installed for decades without any issues. This is a testament to the material’s superior wear resistance and long life. 440C Stainless Steel is more than sufficient for waste water applications, and provides the perfect balance between long cutter life, high reliability and low life cycle cost.
Barnes Sithe Chopper Pumps & Long Lasting Cutter Blades
The Barnes Sithe chopper pumps have a patented open center cutting technology. Cutter blades are made of 440C Heat Treated Stainless Steel and have a hardness of up to 60HRC. Sithe chopper blades can chop and pass hard solids in the waste stream including wood, wire, plastic and small metallic parts. There are hundreds of Sithe chopper installations in extremely demanding waste water applications including correctional facilities, hospitals, zoos, dairy farms and schools where blade sharpness is still pristine even after thousands of hours of operation. Sithe chopper pumps perform a slicing action on solids compared to harsh chopping action. The smooth slicing action exerts less stress on the chopping blades and result in longer cutter life. Accelerated testing of Sithe chopper blades has proved that life expectancy of blades average between 7 and 8 years, and can last as long as 15 years in applications where solids loading is lesser than average. Sithe choppers are designed to have industry lowest clearance of 0.003” to 0.008” between the stationary and rotating blades. These clearances are maintained over years of operation due to hardness of the 440C Heat Treated Stainless Steel. Clearance between blades can be adjusted by adding or removing shims located between the stationary blade and pump suction flange. As a result, Sithe chopper blades can be used for years by just adjusting shims without having to replace the cutters or the pump.
Authors
Jacqueline Boudreau
Director of Product Marketing, CP&S
Sai Venkataramani
Product Manager, CP&S